In tables 1 and 2 we look at a problem where a machine has stopped. In table 1 a blown fuse is identified as the obvious cause for the machine stopping. The immediate solution for this cause is to replace the fuse.
Problem | Cause | Solution |
---|---|---|
The machine has stopped | The fuse blew | Replace the fuse |
In Table 2 we ask "Why?" six times to explore the problem of the machine stopping. This helps us find a different cause behind why the machine stopped.
Question | Answer |
---|---|
1. Why did the machine stop? | Because the fuse blew. |
2. Why did the fuse blow? | Because there was an overload. |
3. Why was there an overload? | Because the bearing lubrication was not adequate. |
4. Why was the lubrication not adequate? | Because the lubricant pump was not working. |
5. Why was the pump not working? | Because the pump axle was worn out. |
6. Why was the axle worn out? | Because sludge got into it. |
Sludge getting into the axle is the root cause of the problem. Replacing the blown fuse will not stop the machine breaking down in future.
Finding the root cause often highlights whole systems or processes that are failing. In the example above the process for managing sludge may need to be improved, rather than just keeping sludge out of the axle.
How to use the tool
- Describe the problem. Try to be specific. What or who does the problem affect? How often does it happen? How long has it been a problem? How much impact does it have?
- Write the problem in the box on the left hand side of a tree diagram like the ones in Figures 1 and 2 and the worksheets in the 'Documents' section on the far right.
- Answer the question: "Why is the problem happening?" These answers are possible causes of the problem.
- Write the causes in the first line of boxes to the right of the problem.
- For each of your first level causes ask again: "Why is this happening?" Write the answers to the right beside the previous causes (like in Figures 1 and 2).
- Try to ask several more consecutive "Why?" questions, to get beyond the symptoms of the problem to the underlying causes.
- When you can think of no more answers to the "Why?" questions, look at all the causes, but particularly the ones on the right hand side.
- Decide which ones are the highest priority. These are the ones that, when fixed, will solve the problem, or reduce it a lot.
- Choose which high priority causes you are going to take action on.
- Develop action plans for the top priority causes.
Examples
Figures 1 and 2 give examples of the Repetitive why technique drawn as tree diagrams. Figure 1 shows causes of low operating profit in a manufacturing business. Figure 2 shows how the technique can be used to identify a root cause.
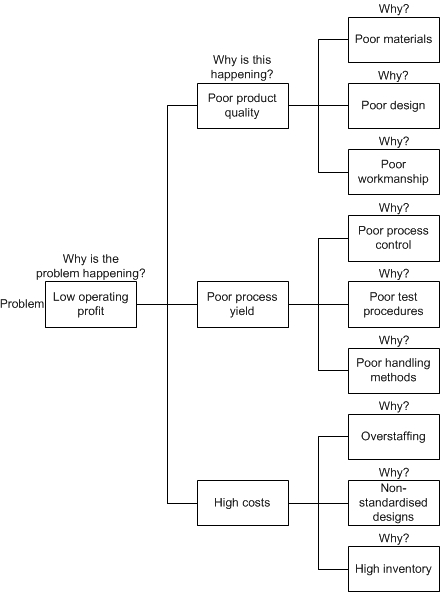
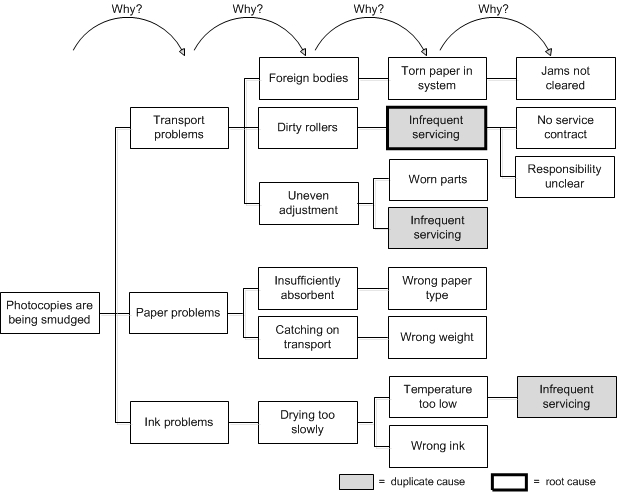
Other tools to use with the Repetitive why technique
The Repetitive why technique can be used in step 2 of the CI&I - Continuous improvement and innovation process.
If there are several high priority causes to choose from and only enough resources to take action on one or two, the Eight criteria technique and Gross margin analysis can be used to compare options.
The Action design tool or Five Ws and one H tool can be used to plan action to tackle a priority cause.
Support to use the tool
Please contact us if you would like help to use the Repetitive why technique.
A worksheet to help you use the technique can be found in the 'Documents' section on the far right.